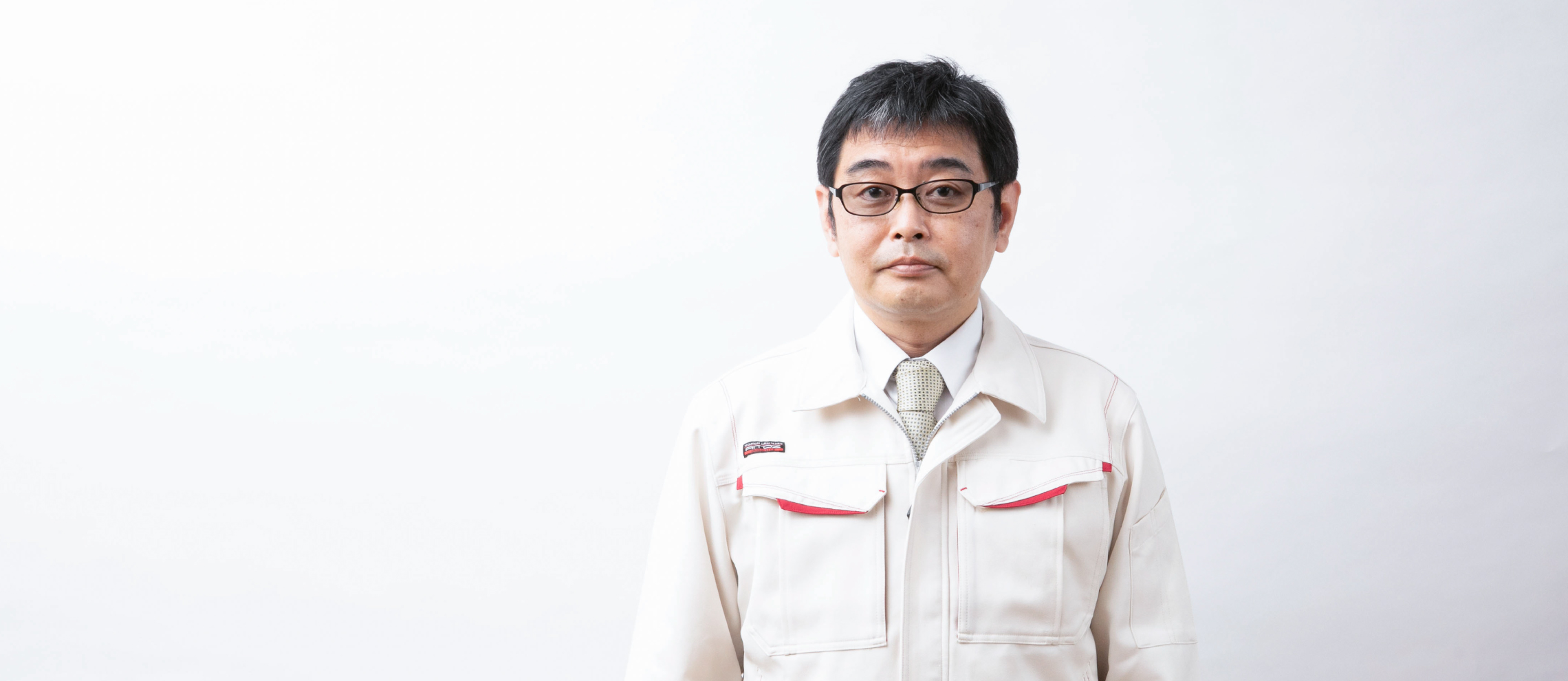
sada
生産技術部 部長代理
半導体設備メーカにて 加工装置研究開発およびプロセス開発に10年間携わったのち、液晶パネル製造メーカにて 生産技術/製造技術を20年間従事。その後、2020年2月にフジデノロ生産技術部、部長代理として中途入社。
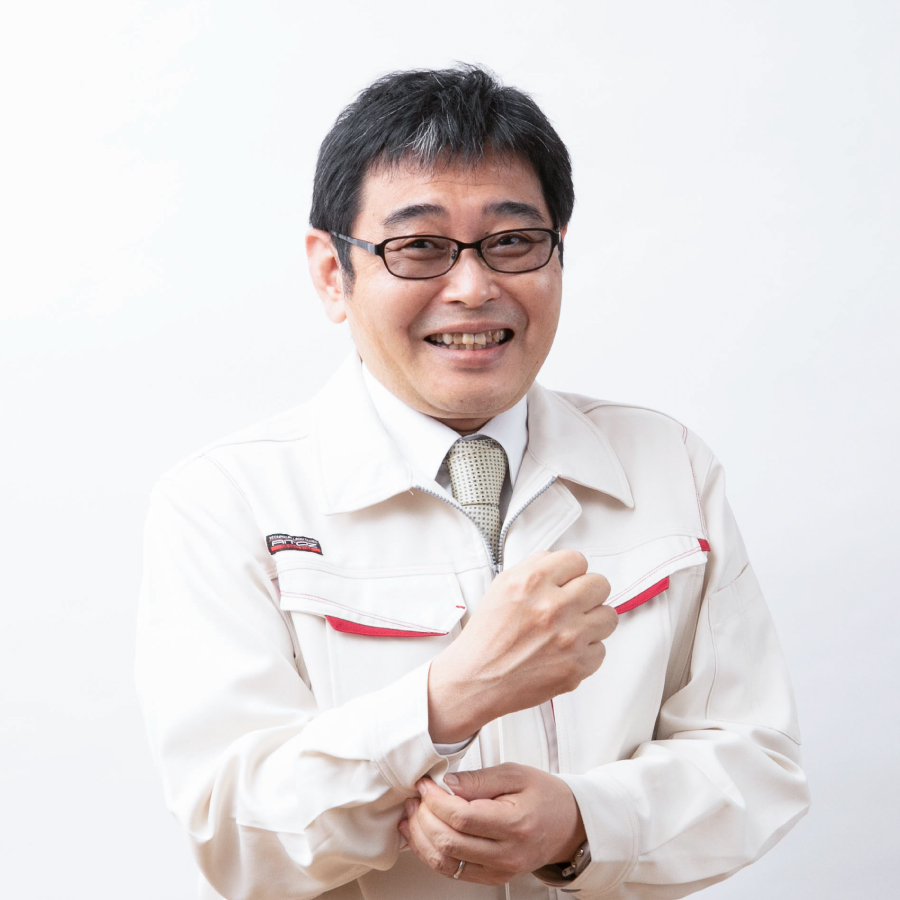
1. 所属部署のミッションと、ご自身が行っている仕事内容を教えてください
主力製品である工業用プラスチック部品の切削加工の製造形態は、多品種小ロット生産であり、現在でも製造作業者による手作業を主力としています。昨今の作業者不足により、加工作業の分担化と省人化が急務となっているため、小ロット生産でありながらも、材料の入替え作業を画一化を目指しています。また、協働ロボットやAGVを用いてワーク搬入出を代行させ、さらに製品・段取りに応じて加工プログラムを自動で切り替えるシステムを開発し、製造ラインへ順次導入を進めています。
2. 仕事の中で、一番やりがいを感じることを教えてください
当社ならではの加工環境(多品種小ロット生産、材料形状・材質、品質管理)によって、世の中に求めたとしても、当社の要求仕様に合致する自動化の仕組みはほとんど存在しません。従って、SIer(構想設計・システム運用設計)としての力量を発揮し、外部の機能機器メーカの助力を得ながら、詳細設計(機械・電気・制御・ソフト)を取りまとめて、最終的に当社にマッチした独自の仕組みを実現できることがやりがいです。
3. これから仕事で新たに挑戦したいことについて教えてください
大型設備を開発する一方で、それらの運用状況の「見える化」にも気を配っています。 加工機自体は日本製(もっと言えば、地場の愛知県メーカ製)でありながら、加工機の自動監視・管理の分野では欧米が先んじて2006年に国際規格標準言語MTConnectが制定され、海外向け出荷装置にだけは標準実装されるなど、日本だけが置き去りにされてしまっています。各メーカごとに異なる切削加工機との遠隔通信方式ならびに情報取得方法(プロトコル、ソフトウェア・ライブラリなど)を調査・勉強しながら、製造作業者が日常業務として台帳管理している稼働記録や稼働状況など、リアルタイムで「見える化」できるシステムを低費用で構築したいと考えています。
4. 入社してから最も大きな「壁」はなんでしたか?また、それをどのように乗り越えましたか?
私自身、今までフライス盤などの切削加工機械とは縁がなかったので、加工機に関わる知識を勉強しながら、加工機の加工品質を含む自動化構想設計・詳細設計を並行して進め、要求機能を数値化することには非常に苦労をしました。その苦労があったおかげで、加工機本体のNCプログラム様式や外部I/Oインターフェース回路、遠隔通信制御仕様、NC制御マクロ言語、NC制御ラダー言語などの知識を短期間で手に入れることができました。
5. 今後フジデノロでどのように成長していきたいですか?目標や夢があれば教えてください
基本的な考えとして、「積み上げが可能な形で新たな機能を残す」を意識してモノづくりを行なっています。会社の規模が大きくなるに連れ、同じ1つの業務のボリュームが増えるのは必然でありますが、それが日常業務であるほどに、従来の手法を継承していただけでは、時間工数的に破綻して放棄してしまうことになりかねません。お客様からの品質および短納期化の要求も年々高くなり、世の中からの要求事項も増加する中、やはりここで重要となるのは、会社員が業務を圧縮し続ける意志を持つことであると考えています。 解決策の1つの方向性として、直接作業者・間接業務者関係なく、素人レベルであっても、データベースやスクリプトを操れる知識を持つこと。このことの認知度を上げていきたいです。